ضرورت بازرسی جوش در قطعه جوشکاری شده این است که انواع نقص ها با اندازه های متفاوت ممكن است در سازه جوشکاری شده وجود داشتــــه باشد، که ماهیت و اندازه دقیق این نقص، کارکرد آتی قطعه را تحت تاثیر قرار می دهد. یکی دیگر از ضرورت ها استفاده از روانساز مناسب هنگام جوشکاری است برای خرید روانکارهای اصل و واورجینال از نمایندگی اس تی پی روی لینک کلیک کنید.
و از طرفی نقص های دیگری مانند ترك های ناشی از خستگی يا خوردگی ، در حین کارسازه نیز ممکن است به وجود آید. بنابراین براي آشکارسازی نقص ها در مرحله ساخت و همچنین برای آشکارسازی و مشاهده آهنگ رشد آنها در حین عمر کاری هر قطعه یا مجموعه باید وسایل قابل اعتمادی در اختیار داشت. همپنین برای انتخاب روانساز مناسب میتوانید به نمایندگی کلوبر مراجعه نمایید.
انواع روش های بازرسی جوش
برای پیشگیری از هر نوع حادثه زیان بار و زیان های اقتصادی در صنایع جوش برای پی بردن به کیفیت جوش از نظر استحکام، سختی، مقاومت و سلامت ، تست جوش را به دو روش، مورد ارزیابی و بازرسی قرار می دهند.
- آزمایش های مخرب (DT)
- آزمایش های غیر مخرب (NDT)
۱) آزمایش مخرب (DT)
آزمایش مخرب یا DT که مخفف کلمه انگلیسی Distractive Test است، به منظور عیب یابی و اطمینان از سلامت جوش با شکستن،کشش، خم کردن قطعه جوش شده را مورد ارزیابی قرار داده و به کیفیت و سلامت آن پی می برند.
۲) آزمایش غیر مخرب (NDT)
آزمایش غیر مخرب یا NDT که مخفف کلمه انگلیسی Non Distractive Test است،قطعات نمونه جوشکاری شده را مورد آزمایش قرار می دهند بدون آنکه خرابی یا تغییر شکل در آنها ایجاد گردد نمودار زیر انواع آزمایش ها را به شما معرفی می کند.
تفاوت های تست DT و NDT
آزمایش مخرب یا DT پس از انجــام آزمایش، قطعه کارایی خود را از دست می دهد ، در روش های DT نمی توان تمام محصولات را تحت آزمایش قرار داد و باید به صورت رندم (انتخابی) تعدادی از نمونه ها را تحت آزمایش قرار داد. در روش های DT نیاز به تهیه نمونه استاندارد وجود دارد که برای آزمایش های مختلف مانند تست کشش ، ضربه و … متفاوت است.
آزمایش غیر مخرب یا NDT روش های غیر تهاجمی در تشخیص سلامتی یک قطعه یا یک سازه جوشکاری شده هستند و در مقایسه با تست های مخرب ، NDT روش تشخیص بدون وارد کردن اسیب ، تنش یا خرابی در آزمایش قطعه است.
معمولاً در آزمایش مخرب یا DT خراب کردن یک جسم هزینه زیادی صرف می شود و در عین حال در بسیاری از موارد قابل توجیح نیست ، از این جهت تست غیر مخرب ،یک روش مهم در بازرسی سلامت سازه بدون آسیب رساندن به آن میباشد. تست NDT در اندازه های بزرگ از فضاهای صنعتی قابل استفاده است و کاربرد گسترده ایی در تست قطعات خودرو، راه آهن، پتروشیمی و خطوط لوله دارد و تست غیر مخرب بیشترین استفاده کاربردی را در جوشکاری دارد.
البتـــه که باید توجه شود آزمایش های DT و NDT در عرض یکدیگر قرار ندارند و انجام یک تست باعث بی نیازی از تست دیگر نمی شود.
آشنایی با روش های تست مخرب
همانطور که در بالاتر اشاره شد آزمایش مخرب یا DT که مخفف کلمه انگلیسی Destructive Testing هستند یک روش برای بازرسی سلامت سازه میباشد ، که بعد از آن سازه غیر قابل استفاده خواهد شد این روش دارای معایب زیر است :
- سرعت پایین
- پر هزینه بودن
- ارائه اطلاعات فقط مربوط به نمونه ها
در بازرسی جوش با روش های مخرب باید چند نمونه با ابعاد و اندازه های مشخص ساخته شود و با توجه به توصیه های استاندارد مربوطه قطعات آزمایش شوند .
انواع روش های تست مخرب
۱) آزمایش خمش
آزمایش خمش یا Bend Test یک تست ارزان قیمت و ساده میباشد ، که میتوان شکل پذیری و سلامت جوش با لحاظ عدم وجود تخلخل و ناخالصی در جوش {عیوب جوش} مورد ارزیابی قرار داد ، این روش بیشتر برای تست قطعات جوشکاری شده لب به لب یا Butt Joint { انواع اتصلات جوشی } مورد استفاده قرار میگیرد . چون این روش نیاز به تجهیزات پیچیده ندارد و آماده سازی نمونه سریع انجام میشود ، یک روش پر بازده در کارگاه های تولیدی می باشد .
در آزمایش خمش ابتدا نمونه با توجه به استاندارد مربوطه ساخته و سپس ریشه جوش و گرده جوش را سنگ می زنند و پس از آماده شدن نمونه آن را در دستگاه تست خمش قرار داده و به بصورت U انگلیسی در می آورند. در این روش نمونه را طوری در ماشین خمش قرار می دهند تا محل جوش کاملا در وسط دستگاه خمش قرار گیرد . در این روش جوش موقعی قابل قبول خواهد بود که ترک یا عیب دیگری در نمونه مورد نظر از ۴ میلی متر یا حداکثر از نصف ضخامت نمونه تجاوز ننماید.
این روش تست را هم می توان برای گرده جوش و هم ریشه جوش و هم اطراف جوش (منطقه متاثر از حرارت HAZ) استفاده کند .
۲) آزمایش کشش
در آزمایش کشش نمونه هایی به طول حدود ۲۰ سانتی متر و عرض ۵/۲ الی ۳ سانتی متر ساخته و آنها را در دستگاه کشش تا حد پارگی تحت نیروی کشش قرار می دهند در صورتی که مقاومت کششی جوش مساوی یا بیشتر از حداقل مقاومت کشش فلز مبنا باشد آزمایش قابل قبول بوده و در غیر این صورت دستورالعمل جوشکاری مردود شناخته خواهد شد. تست کشش یکی از روش های متداول بازرسی جوش با تست مخرب است . که معمولاً برای بررسی و تست کیفیت جوش مورد استفاده قرار می گیرد .
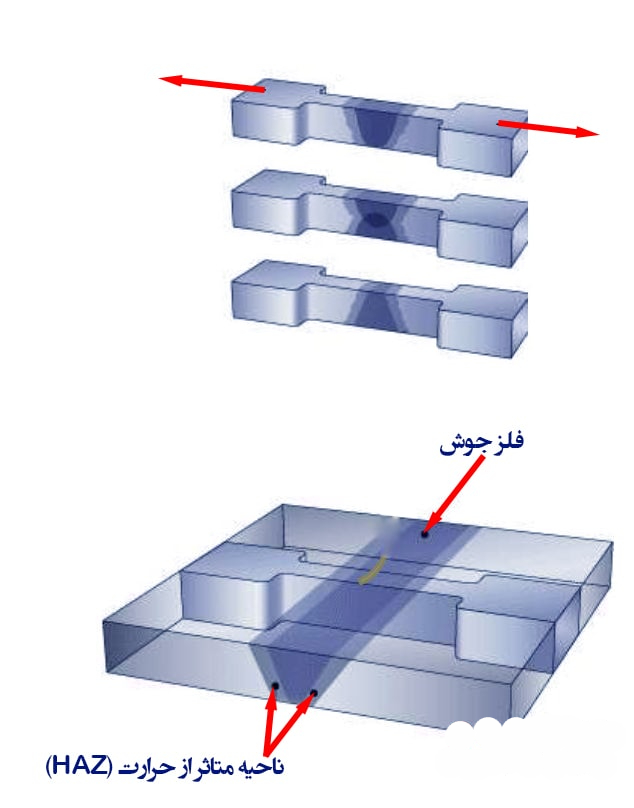
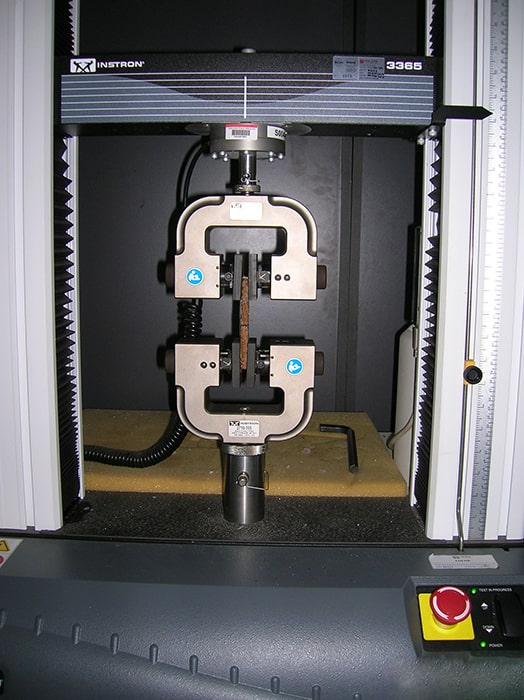
۳) آزمایش ضربه
تست ضربه یا Impact test یک آزمایش برای ارزیابی چقرمگی شکست قطعات میباشد که معیار آن انرژی لازم برای شکست نمونه بر حسب ژول میباشد .اصول کلی آزمایش ضربه به این صورت است که پاندول دستگاه به اندازه که برای انرژی لازم برای شکست بالا برده میشود و سپس بصورت ناگهانی رها میشود و سپس بر اساس اینکه چه میزان پاندول از موقیت ابتدایی تا موقعیت انتهایی بالا آمده است مقدار انرژی جذب شده برای شکست محاسبه میشود . در این تست دما نقش بسیــار مهمی را ایفا میکند . دو روش متداول برای انجام این آزمایش وجود دارد
- تست ضربه شارپی
- تست ضربه ایزود
تست ضربه شارپی و تست ضربه ایزود
تست ضربه شارپی Charpy Impact Test متداول ترین روش ارزیابی چقرمگی شکست قطعات است ، که قطعه بصورت وی شکل شیار زده میشود (Vee-Notch) و اعمال ضربه از پشت محل شیار زده شده توسط پاندول انجام میشود .
تست ضربه ایزود Izod Impact Test معمولاً در دمای اتاق انجام میشود و نحوه شیار زدن قطعه مشابه تست ضربه شارپی است و فقط با این تفاوت که اعمال ضربه از جلوی محل شیار زده شده توسط پاندول انجام میشود .
در این روش اگر نیروی متحمله برای شکست مقاطع مورد نظر بیشتر یا مساوی فلز مبنا باشد جوش قابل قبول و در غیر این صورت مردود شناخته خواهد شد.
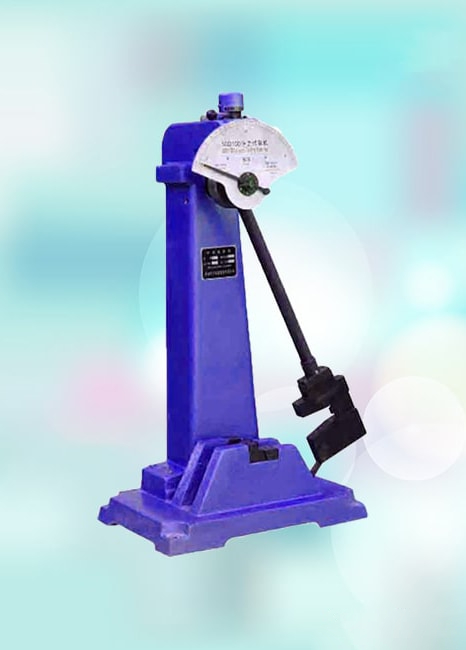
آشنایی با روش های تست غیر مخرب
در بازرسی جوش با روش های غیر مخرب تست Non-destructive testing قطعه کار آسیب نمی بیند و برعکس بازرسی جوش مخرب که قطعه آسیب می دید در این روش ها قطعه تخریب نمی شود . تا کنون روش های مختلفی برای انجام تست غیر مخرب NDT توسعه یافته اند که برخی از مهمترین آنها بشرح زیر است .
نکته در این مقاله خلاصه ایی از روش های بازرسی جوش بر روش غیر مخرب توضیح داده میشود برای مطالعه کامل تر این بخش لطفاً اینجا { سیر تا پیاز تست غیر مخرب NDT } کلیک کنید .
انواع روش های تست غیر مخرب
۱) تست چشمی (VT)
بازرسی چشمی که با علامت (V. T) در این صنعت معرفی و شناخته می شود. یکی از مهم ترین و متداول ترین روش بررسی است.
این روش بازرسی ساده و قابل دسترس و ارزان می باشد و به دستگاه گران قیمت نیار ندارد . در این روش تمام عیوب ظاهری اعم از عیوب سطحی ، نادرستی مونتاژ و شکل کار و انحراف در اندازه ها و …. را میتوان جستجو و پیدا کرد .
ابزار مورد استفاده در این روش بازرسی عبارتست از:
- گیج چند کاره
- ذره بین با بزرگنمایی ده برابر
- وسایل اندازه گیری
- الگو با شابلن مخصوص
- چراغ سیار یا چراغ قوه
- فایبر اسکوپ (Fiber-scope)
- بوروسكوب (Bore-scope)
نکات مهم در بازرسی چشمی (VT) جوش
در این روش نیاز به کارشناس یا بازرس جوش خبره و با تجربه برای بازرسی چشمی جوش هستیم و مهم ترین ویژگی که یک بازرس جوش ، چشمی باید دارا باشد چشم تیزبین و عقل سلیم است و رمز موفقیت در بازرسی چشمی داشتن آگاهی از مشخصات فنی و توانایی تصمیم گیری در مورد پذیرش یا عدم پذیرش محصول است و در هیچ زمانی این روش بازرسی نباید کم اهمیت تلقی شود .
بازرسی چشمی صحیح قطعات و بررسی شکل ظاهری آنها چه با چشم غیر مسلح و چه با ذره بین یا اندوسکوپ انجام شود در تشخیص عیوب متالوژیکی حائز اهمیت است و می تواند مبنای برنامه ریزی برای بازرسی های بعدی باشد.
با توجه به توضیحات فوق بازرسی چشمی جوش در سه مرحله انجام می گیرد
- قبل از جوشکاری
- حین جوشکاری
- بعد از جوشکاری
بازرسی چشمی (VT) جوش چه اطلاعتی را در اختیار ما می گذارد ؟
بازرسی چشمی در هنگامی که جوشکاری انجام می شود و بعد از آن باعث بالا رفتن کیفیت جوش می شود و بعد از تکمیل آن، اطلاعات زیر را در اختیار بازرس می گذارد.
- آیا نفوذ و ذوب به صورت کامل بین فلز پایه و فلز جوش انجام گرفته؟ برای اطلاعات بیشتر مقاله [ ۰ تا ۱۰۰ عیوب جوش ] مطالعه شود .
- آیا نشانه ای از وجود سوختگی لبه جوش در امتداد مرز جوش و فلز پایه وجود دارد؟ برای اطلاعات بیشتر مقاله [ ۰ تا ۱۰۰ عیوب جوش ] مطالعه شود .
- با نگاه کردن به ریشه جوش های V یا U شکل می توان فهمید ایا نفوذ در اتصال به میزان لازم انجام شده؟
- آيا گرده جوش حالت مناسب (محدب) دارد یا حالت مقعر دارد؟ توجه داشته باشید که در حالت مقعر، به علت عدم وجود فلز جوش لازم در گرده جوش، باعث ضعیف شدن جوش می گردد.
- آیا ابعاد جوش درست می باشد؟
- مطابقت جوش ها با اندازه های تعیین شده آماده سازی ها و کنترل مراحل آماده سازی جوش
- قابل قبول بودن ظاهر جوش با توجه به عواملی مانند ظاهر گرده جوش، پاشش های جوش، سوختگی لبه جوش و روی هم افتادگی جوش
- مشاهده عیوب و ترک ها در سطح قابل مشاهده جوش
- عدم نفوذ در ریشه یا نفوذ بیش از اندازه در ریشه
- سوراخ های کوچک ولی عمیق، حفره های گازی، تورق در انتهای ورق
- حالت غیر طبیعی موج های گرده جوش و…
در گزارشی که بعد از پایان بازرسی چشمی جوش یا بازرسی VT در اختیار کار فرما قرار می گیرد ، تمامی اطلاعات فوق درج می شود .
۲ ) تست غیر مخرب با مواد نافذ PT
روش بازرسی با مواد نفوذ کننده یا PT برای آشکار سازی نقص هایی است که سبب شکستن سطح کار شده اند ، توجه داشته باشید که با روش بازرسی با مواد نفوذ کننده فقط عیوبی قابل تشخیص هستند که به سطح قطعه کار راه پیدا کرده اند .
این روش مبتنی بر جذب موئینگی مايع به درون نقص است و بدین ترتیب پس از ظهور ، تمامی شکستگی ها سطحی با چشم دیده خواهد شد.
منشا واقعی این روش ناشناخته است اما سابقا برای آشکارسازی ترک های لعاب از دوده بر روی سفالینه های لعابی استفاده می کردند . امروزه بازرسی با مایع نافذ PT ، روش صنعتی مهمی است و برای تعیین نقص هایی مانند :
- ترک ها
- روی هم افتادگی
- منطقه های تخلخل سطحی
- و ….
این روش تقریباً برای همه قطعات قابل استفاده است اعم از این که قطعه بزرگ باشد با کوچک، شکل ساده داشته باشد یا پیچیده باشد . این روش برای بازرسی قطعات ریختگی ، قطعات فورجینگ و بازرسی جوش مورد استفاده قرار می گیرد .
اصول بازرسی با مواد نفوذ کننده PT
روش بازرسی با مواد نافذ پنج مرحله اساسی دارد و عبارتند از:
- آماده سازی سطح
- کاربرد مواد نفوذ کننده
- زدودن مواد اضافی
- استفاده از ظاهر کننده ها و بازرسی
روش بازرسی با مواد نفوذ کننده یا PT به شرح زیر است .
- مایع نافذ بر روی سطح قطعه برای مدت معینی اعمال می شود.
- مایع نافذ درون عيوب توسط خاصیت موئینگی نفوذ می کند.
- اضافی مایع نافذ از روی سطح جمع آوری می شود.
- سطح خشک می شود و ماده ظهور اعمال می شود.
- مایع نافذی که در داخل عيوب باقی مانده توسط ماده ظهور جذب می شود
- وجود، محل، اندازه و نوع عیب نشان داده می شود.
بهترین و اقتصادی ترین روش آزمایش با مایعات نافذ بستگی به ابعاد و تعداد قطعات دارد.
نکات مهم در روش بازرسی با مایع نافذ PT
- عیوبی را که سطحی نیستند (یا به سطح راه ندارند) یا در حالت غیر مرئی (چه با چشم غیر مسلح، چه با اندوسکوپ) واقع شده اند آشکار نمی کند.
- عیوب خیلی کوچک را که ماده رنگی به داخل آن نفوذ نمی کند یا بقدر کافی نفوذ نمی کند پیدا نمیکند . آزمون مایعات باید برای بررسی سلامت سطح در موارد زیر مناسب نیست .
- قطعات متخلخل
- قطعات ریخته شده با چدن
- بعضی قطعات دقیق فولاد
- قطعات هندسی خیلی پیچیده
بخاطر خصوصیات سطحی خود اگر با مایعات نافذ آزمایش شوند علایم صحیح نشان نمیدهد .
۳) تست غیر مخرب با مواد مغناطیسی MT
یکی از شیوه های متداول بازرسی جوش ، مخصوصاً مخازنی که تحت فشار واقع می شوند تست غیر مخرب ذرات مغناطیسی MT است .
در روش تست MT قطعات جوش خورده را موقتاً مغناطیسی کرده و سپس براده آهن روی درز آن می پاشند و شکاف ها و ترک ها و سوراخ های موجود در درز هرچقدر هم کوچک باشد از روی پراکندگی براده ها معلوم می شود. این شیوه را فقط در آزمایش فلزاتی که آهن ربا می شوند می توان بکار برد .
ترک یابی مغناطیسی، میدان های نشت سطحی آشکارپذیر که توسط نقص موجود در سطح به وجود آمده اند.
بازرسی به وسیله تست غیر مخرب ذرات مغناطیسی MT روش بسیار حساسی می تواند باشد اما چندین عامل بر این حساسیت تأثیر می گذارند. عامل مهمی که قبلا به آن اشاره شد، موقعیت ناپیوستگی نسبت به میدان مغناطیسی القائی است و اگر ترک بر میدان عمود باشد حساسیت بالاتر خواهد بود. عامل های مهم دیگر عبارتند از اندازه، شکل و مشخصه های کلی ذرات مغناطیسی به کار رفته و همچنین سیال حامل بر این ذرات این روش محدود به مواد مغناطیس شونده نظیر چدن و فولاد بوده و برای مواد و فلزات غیر مغناطیسی مانند فولاد ضد زنگ، آلومینیوم و مس کاربرد ندارد.
به وسیله تست غیر مخرب ذرات مغناطیسی MT و با استفاده از یوک و پراد می توان بسیاری از عیوبی که به سطح راه پیدا کرده اند را شناسایی کرد (این عیوب شامل ترک های سطحی، ذوب ناقص، تخلخل، بریدگی کناره جوش، نفوذ ناقص ریشه جوش و … ){۰ تا ۱۰۰ عیوب جوش }
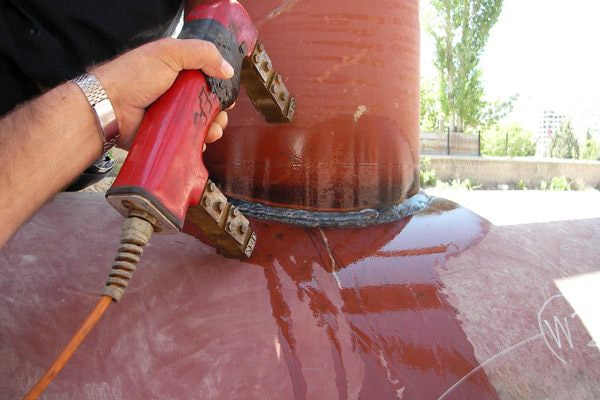
۴) تست غیرمخرب رادیوگرافی
پرتونگاری یا رادیو گرافی که با علامت ( R . T) معرفی و شناسایی می شود یکی از روش های آزمایش غیرمخرب می باشد که نوع و محل عیوب داخلی و بسیار ریز جوش را نشان می دهد، در پرتونگاری با اشعه X یا اشعه مجهول از خاصیت نفوذ آن در اجسام و جذب نسبی اشعه توسط اجسامی که از آنها عبور می کنند و نیز اثر اشعه بر روی فیلم های حساس اشعه X و گاما استفاده می کنند. پس از اتمام رادیوگرافی فیلم را ظاهر نموده و تصاویر اجسام را روی فیلم ها مورد ارزیابی قرار میدهند.
پرتونگاری مانند بیشتر امور فنی دارای محدودیت هایی است که بکارگیری و فهم درست و تفسیر آن و به دانش فنی و تصور صحیح عیب و رابطه آن با مشخصه علمی دارد و آگاهی از جنس و ضخامت فلز مورد پرتونگاری و مطابقت آن با قدرت نفوذ منبع رادیواکتیو مورد استفاده حایز اهمیت فراوانی است .
منبع تست رادیوگرافی R.T معمولاً یا با استفاده از اشعه گاما یا اشعه ایکس تامین میشود . برای تولید اشعه گاما از مواد پرتو زا استفاده میشود و برای تامین شعه ایکس از لامپ مولد اشعه ایکس استفاده میشود . که هر دو برای سلامتی انسان بشدت مضر هستند و باید موارد ایمنی را رعایت کرد.
خواص عمده اشعه ایکس و گاما
- از نوع امواج الکترومغناطیس می باشد
- فاقد جرم است.
- با سرعت نور در خط مستقیم حرکت می کن
- تحت تاثیر میدان های مغناطیسی و الکتریکی قرار نمی گیرد
- از تمام مواد موجود در طبیعت عبور می کند
- باعث یونیزه شدن گازها و از بین بردن سلول های زنده می شود
- بر روی صفحات حساس اثر گذاشته و موجب سیاه شدن آنها پس از ظهور میگردد .
تست رادیوگرافی RT برای چه موادی کاربرد دارد ؟
اشعه X تقریبـــاً از تمام مواد نفوذ می کند و به تناسب ضخامت ماده ای که از آن می گذرد ضعیف میشود جنس ماده ای که اشعه X بر آن می تابد نیز در تضعیف آن مؤثر است به عنوان مثال آهن بیشتر ازآلومینیوم و کمتر از مس از شدت اشعه X را می کاهد و صفحه سربی به ضخامت مشخص کلاً را عبور اشعه X را محدود میکند .
یکی از خواص اشعه X این است که مانند نور روی قشر شیمیایی فیلم عکاسی تاثیر می کند و پس از ظهور فیلم نقاطی از آن که تحت تأثیر اشعه X قرار گرفته سیاه می شود.
حال اگر اشعه X را از قطعه فلزی که دارای عیوب جوش مانند (تخلخل ، ترک و… ) عبور دهیم، در این نقاط بر حسب شكل و وضع آنها کم و بیش ضعیف می شود و در نتیجه روی نقاط فیلمی که زیر آن قطعه قرار گرفته به شدت مختلف تأثیر می گذارند ، بدین ترتیب می توان درز جوش خورده فلزات را بدون شکستن یا خراب کردن آنها به سرعت آزمایش کرد و نقایص و معایب آن را تعیین کرد .
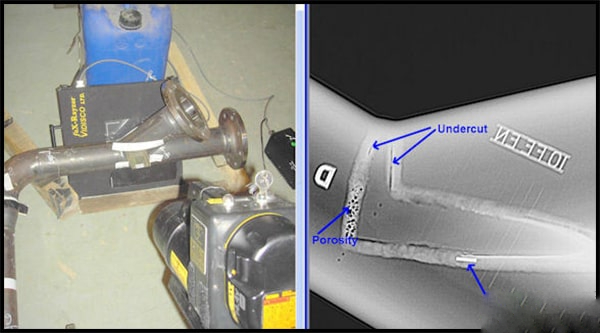
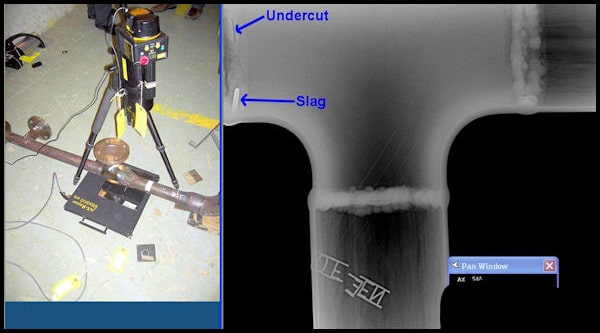
۵) تست غیر مخرب التراسونیک UT
تست غیر مخرب التراسونیک UT ، یکی دیگر از روش های متداول در بازرسی جوش است . ارتعاشات مافوق صوت با التراسونیک به نوساناتی گفته می شود که فرکانس آنها بیش از حداکثر فرکانسی است که گوش انسان قادر به شنیدن آن است. زیرا گوش انسان قادر به شنیدن نوسانات بین ۱۵ بار در ثانيه الى ۲۰۰۰۰ بار در ثانیه (هرتز) می باشد.
نوسانات بالای ۲۰۰۰۰ بار در ثانیه را ارتعاشات مافوق صوت می نامند . چون ارتعاشات مافوق صوت به آسانی در جامدات منتشر می گردند در نتیجه اگر ارتعاش مافوق صوتی به سطح یک جسم جامد اعمال گردد در قسمت درونی آن با سرعتی که بستگی به فشردگی و جنس آن جسم دارد منتشر گردیده و هرگاه به مانع یا سطح جداکننده ای برخورد نماید بازتاب آن منعکس خواهد شد در نتیجه می توان با ضبط این بازتاب ها به وسیله دستگاه های مخصوص به نواقص درونی و نیز به ضخامت جسم پی برد.
کلمه التراسونیک از دو واژه الــترا + سونیــک تشکیل شده است الترا در کلمه التراسونیک به مفهوم زیاد و سونیک معنی امواج صوتی یا ارتعاش دارد.
کاربرد تست غیر مخرب التراسونیک UT
تست غیر مخرب التراسونیک UT را می توان به علت ویژگی های بنیادی اش برای آزمایش قطعات مختلف ساخته شده فلزی و غیرفلزی مانند بازرسی جوش ، بازرسی قطعه های آهنگری یا ریخته شده، ورق، لوله، پلاستیک، سرامیک و … به کار برد.
از آنجا که آزمون فراصوتی برای آشکارسازی عیب های زیر سطحی روشی کم هزینه است، یکی از مؤثرترین ابزارهای موجود برای کسانی است که در بخش کنترل کیفیت مشغول انجام وظیفه هستند. تست غیر مخرب التراسونیک UT افزون بر بازرسی قطعات تکمیل شده، برای بازرسی کنترل کیفیت مراحل مختلف تولید قطعاتی همچون لوله های نورد شده نیز بکار می روند و از این روش ها برای بازرسی قطعات و مجموعه های در حین کار نیز استفاده می شود.
اساس روش کار تست التراسونیک UT
آزمایش با تست غیر مخرب التراسونیک UT با استفاده از یک مبدل ( مبدل پیزوالکتریک ) که مشابه یک موج صوتی ولی با گام و فرکانس بالاتری است انجام می شود.
موج های فراصوتی از داخل قطعه مورد آزمایش عبور داده می شوند و با هرگونه تغییر در تراکم داخلی قطعه منعکس می شوند. این موج ها توسط یک مبدل که تحت جریان AC قرار دارد و به یک واحد جستجوگر متصل شده تولید می شوند. امواج منعکس شده یا پژواک ها به صورت برجستگی هایی نسبت به خط مبنا بر روی صفحه نمایش دستگاه ظاهر می شوند. هنگامی که واحد جست وجوگر به قطعات مورد بازرسی مورد نظر متصل شود دو نوع پژواک بر روی صفحه نمایش ظاهر می شود. ضربان اول انعکاس صدا از سطح رویی جسم که در تماس با دستگاه است می باشد و ضربان دوم مربوط به انعکاس موج از سطح مقابل است.
نحوه تشخیص عیب در تست التراسونیک UT
همانطور که اشاره شد در ابتدا یک موج ارسال می شود و سپس بازتاب آن توسط گیرنده دریافت می شود و فاصله بین این دو ضربان با دقت کالیبره می شود. این الگو نشان می دهد که قطعات مورد بازرسی آیا سالم هستند یا خیر ؟!
هنگامی که یک عیب یا ترک داخلی توسط واحد جست و جو پیدا شود، تولید اکو یا موج سومی می کند که بین ضربان اول و دوم بر روی صفحه نمایش ثبت می شود. مانند شکل زیر بنابر مشخص می شود که محل این عیب بین سطوح بالا و پایین مصالح (در داخل جسم مصالح) می فاصله میان ضربان و ارتفاع نسبی آنها محل و میزان سختی (تراکم) عیب مزبور را مشخص می کند .
در با تست غیر مخرب التراسونیک UT بعضی از عیوب مثل دانه بندی های درشت و نابجایی ها و عیوبی نظیر وجود ناخالصی ها و ذرات خارجی منظم در یک قطعه اگر اندازه آنها نسبت به طول موج فرستاده شده کوچک باشد ممکن است شناسایی نشوند .
کوتاه کردن طول موج به وسیله اضافه کردن فرکانس باعث جذب بیشترامواج خواهد شد در نتیجه جزئی ترین عیوب در ساختمان یک قطعه، به وسیله اندازه گیری جذب امواج فرستاده شده در آن قطعه می تواند مورد شناسایی و بررسی قرار گیرد.
تست التراسونیک پیشرفته فیزاری phased array
تست غیر مخرب التراسونیک UT سنتی دارای برخی از محدودیت ها مانند سرعت پائین در پردازش اطلاعات ، عدم حساسیت به ترک های ریز ، نیاز به کوپلنت و …. است . این محدودیت ها سبب شده است تا محققین در صدد بر طرف کردن این محدودیت ها بر بیایند .
تست التراسونیک پیشرفته موفق شده است تا حدودی این محدویت ها را جبران کند ، در مقاله [ سیر تا پیاز تست التراسونیک UT ] ما دو روش تست التراسونیک پیشرفته را مورد بررسی قرار داده ایم که می توانید مطالعه کنید .
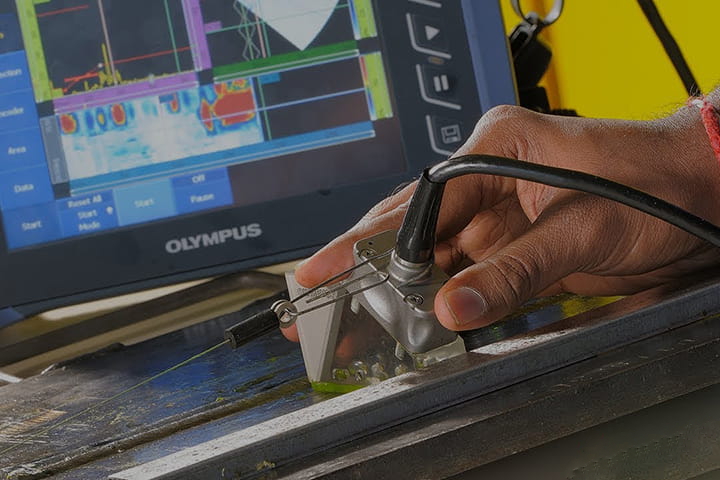
تست نشتی یا LT
تست نشتی LT یکی دیگر از تست های مورد استفاده در بازرسی جوش است . تست نشتی LT بصورت گسترده در در بازرسی مخازن تحت فشار مورد استفاده قرار می گیرند .
تست LT که مخفف کلمـــه انگلیسی Leak Testing است ، یکی دیگر از زیر مجموعه روش تست غیر مخرب NDT می باشد .این روش برای تشخیص وجود درز یا شکاف در قطعه و همچنین تعیین اندازه آن مورد استفاده قرار می گیرد .
تست نشتی یا LT به چند روش قابل انجام می باشد که برخی از آنهـــا ساده و برخی نسبتــاً پیچیده هستند . که تمام روش های موجود را می توانید در مقالــه [ آشنایی با تست نشتی یا LT به زبان ساده ] مطالعه بفرماید .
اساس روش تست LT یکی هستند در روش ساده مخزن با یک فشار مشخص از گاز پر می شود و سپس در داخل یک مخزن سیال غرق می شود و اگر حبابی در داخل مایع دیده شد نشان دهنده وجود نشتی در داخل مخزن است .
روش دیگر تست LT به این صورت است که با استفاده از فشار سنج ، فشار داخلی و خارجی مخزن اندازه گیری می شود و این کار را در طی یک مدت زمان مشخص ثبت و ضبط کرده و اگر پس از مدت زمان معینی فشار مخزن کاهش چشمگیری را نشان داد نشان دهنده وجود نشتی در مخزن است .
تست آکوستیک امیشن
تست آکوستیک امیشن یا نشرآوایی یکی دیگر از تست هایی است که در بازرسی جوش زیاد مورد استفاده قرار می گیرد . شاید در بازخورد اول به علت ناآشنایی با نام تست آکوستیک امیشن فکر کنید که این روش تست کاربرد زیادی ندارد اما باید گفت که تست تست آکوستیک امیشن یا نشرآوایی یکی از تست های اصلی در بازرسی مخازن تحت فشار و سازه های جوشکاری شده عظیم می باشد .
آکوستیک امیشن یا نشر آوایی (AE) که مخفف کلمه انگلیسی Acoustic Emission است با استفاده از سینگنال آکوستیک فرکانس بالا و ضبط آنها و پردازش سینگال از کیفیت و وضیعت سازه جوشکاری شده آگاه می شویم .
برای اطلاعات بیشتر در مورد تست اکوستیک امیشن ، مقاله [ ۰ تا ۱۰۰ آکوستیک امیشن یا نشر آوایی ] را مطالعه فرمائید .
برای اطلاع از۷ آلیاژ مهم فولاد روی لینک کلیک کنید.